The pressure is on! And it's such a relief!
A few weeks ago the blog was all about finally getting the Alfatross up on the rotisserie so it could be soda blasted and move to the next preparation stage. This post is about why it has taken so long to get back to that. Soda blasting needs three things: soda, a rotisserie, and plenty of compressed air. Make that four things: add cooperative weather. A month ago I had all four--briefly--and the result was rapid progress stripping the old paint and filler off the Alfatross' body. But the diesel-powered compressor was rented ($200/day!) and this time of year in Northern New Mexico the weather can't decide if it is winter or summer. The only thing you can count on is the wind: plenty of it and all day long.
Suffice it to say that there were delays . . . .
Speaking of wind, I knew I needed to replace my aging, feeble, low-volume, low pressure reciprocating air compressor with something more robust. Soda blasting doesn't need all that much pressure, maybe only about 100 PSI. But it does need volume--like something north of 30 CFM! Just to put that in perspective, a telephone booth (anybody still remember them?) has a volume of about 80 cubic feet. So a compressor capable of producing 30 cubic feet of air per minute at 100 PSI (which is 6.8 times normal air pressure at sea level) could fill 2 1/3 telephone booths per minute. It would take you about 5 hours to breath that much air . . . and the compressor has to make it in one minute!
OK, that didn't sound as impressive as I thought it would. What IS impressive is what compressors like that cost! In the first place volume and pressure are only two of many considerations when you're compressor shopping. The next consideration in importance for me was noise.
Your typical "reciprocating" shop compressor uses an electric motor to move pistons or diaphragms to compress air, like an internal combustion engine turning over on its electric starter before ignition takes place. They can be deafening.
Other considerations include power consumption (or "efficiency"), space needed, configuration of storage tank (vertical or horizontal), duty cycle design specification, and of course maintenance costs.
Reciprocating and "rotary screw" compressors are the most common types, but I ran across another variant called "Hydrovane" that intrigued me. Reciprocating compressors that would do the job were out of the question because the racket they would make in my little shop would be unbearable. Rotary screw jobs are great, but one that could make the pressure and volume I was looking for would cost close to $10,000! The hydrovane boasted direct drive (no belts), low rotational speed, low noise, continuous duty, improved efficiency over time (!?), and lower cost (more like $4,000 before shipping, etc.).
I was immediately attracted to the Hydrovane principle because it reminded me of the rotary engine in my Mazda RX-8 in reverse. In both cases you have rotors instead of pistons as the only moving parts,and chambers instead of cylinders (the Hydrovane calls them "stators").
Here's where it gets interesting. His guys did the job in 2 hours, but I still had to wait for WISCO to send a start up team up from Albuquerque to look the system over for warranty purposes.
Long story short, WISCO's guys drove the 70 miles up from Albuquerque, inspected everything, threw the switch--and promptly blew the two gigantic main fuses in the compressor's control box! Turns out they were special. You can't find fuses like that in Santa Fe. So they drove the 70 miles back to Albuquerque and returned the next day with the proper replacements. After mulling things over, they realized that Serrano's electricians had connected line power to the wrong place in the control box. I don't know why they missed that the first time. They rewired it, threw the switch again--and the Hydrovane sprang to life at last! It was smooth, it was quiet, and automatically cut off at 150 PSI. Perfect--except for the fact that I had to pay twice as much for the electrical work done by two different groups of electricians, each of which made bad mistakes.
Maybe they both should advertise: "We charge twice as much to do it wrong the first time!"
Caveat Emptor!
A few weeks ago the blog was all about finally getting the Alfatross up on the rotisserie so it could be soda blasted and move to the next preparation stage. This post is about why it has taken so long to get back to that. Soda blasting needs three things: soda, a rotisserie, and plenty of compressed air. Make that four things: add cooperative weather. A month ago I had all four--briefly--and the result was rapid progress stripping the old paint and filler off the Alfatross' body. But the diesel-powered compressor was rented ($200/day!) and this time of year in Northern New Mexico the weather can't decide if it is winter or summer. The only thing you can count on is the wind: plenty of it and all day long.
Suffice it to say that there were delays . . . .
![]() |
So this is what I went to school all those years for? |
Speaking of wind, I knew I needed to replace my aging, feeble, low-volume, low pressure reciprocating air compressor with something more robust. Soda blasting doesn't need all that much pressure, maybe only about 100 PSI. But it does need volume--like something north of 30 CFM! Just to put that in perspective, a telephone booth (anybody still remember them?) has a volume of about 80 cubic feet. So a compressor capable of producing 30 cubic feet of air per minute at 100 PSI (which is 6.8 times normal air pressure at sea level) could fill 2 1/3 telephone booths per minute. It would take you about 5 hours to breath that much air . . . and the compressor has to make it in one minute!
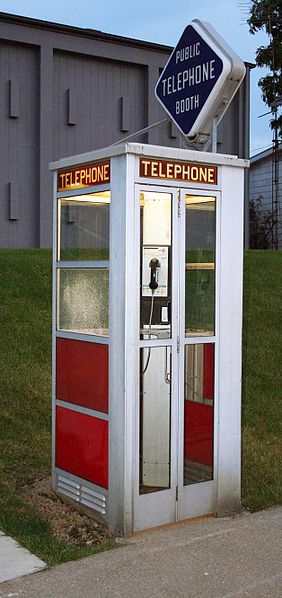
Your typical "reciprocating" shop compressor uses an electric motor to move pistons or diaphragms to compress air, like an internal combustion engine turning over on its electric starter before ignition takes place. They can be deafening.
Other considerations include power consumption (or "efficiency"), space needed, configuration of storage tank (vertical or horizontal), duty cycle design specification, and of course maintenance costs.
Reciprocating and "rotary screw" compressors are the most common types, but I ran across another variant called "Hydrovane" that intrigued me. Reciprocating compressors that would do the job were out of the question because the racket they would make in my little shop would be unbearable. Rotary screw jobs are great, but one that could make the pressure and volume I was looking for would cost close to $10,000! The hydrovane boasted direct drive (no belts), low rotational speed, low noise, continuous duty, improved efficiency over time (!?), and lower cost (more like $4,000 before shipping, etc.).
I was immediately attracted to the Hydrovane principle because it reminded me of the rotary engine in my Mazda RX-8 in reverse. In both cases you have rotors instead of pistons as the only moving parts,and chambers instead of cylinders (the Hydrovane calls them "stators").
Here's where it gets interesting. His guys did the job in 2 hours, but I still had to wait for WISCO to send a start up team up from Albuquerque to look the system over for warranty purposes.
![]() |
Miguel Serrano's guys swarming all over the Hydrovane, wiring it in to code. 220V appliances need to be taken seriously! |
Maybe they both should advertise: "We charge twice as much to do it wrong the first time!"
Caveat Emptor!
![]() |
Ready for action at last. More power! More air! Small footprint and very quiet. Highly recommended--just make sure it's wired in right to start with! |